In construction, crushing refers to applying a large amount of force with a mechanical advantage through an item composed of molecules bound together. The process aims to reduce the size for the realization of other types of products like small rocks, sand, and rock dust. Such items get employed in various construction sites or to allow for easy disposal. There are a variety of crushing devices all suitable for various circumstances as they operate on different principles. Below is a compilation of the types of crusher plant and their uses.
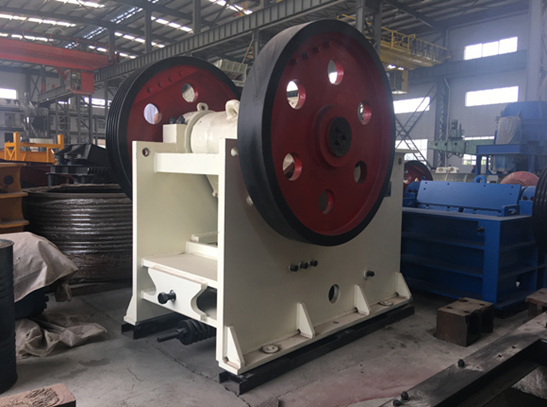
Jaw Crushers.
Jaw crushers are the standard and basic types that you mostly spot in sites. They are popular since they play the role of preparing the materials for the next advanced crushing level. Its structure assumes two types of jaw, one is movable and the other fixed. The model comes in further two designs, a single or double toggle jaw crusher. The individual toggle model works by utilizing an eccentric shaft fitted on top of the crusher. It rotates hence causing a compressive action that breaks the rock. The other model has two rods and plates. The crushing surface is extensive, thus accommodating a large quantity. However, working with a single toggle is more convenient as crushing occurs at intake and discharge levels.
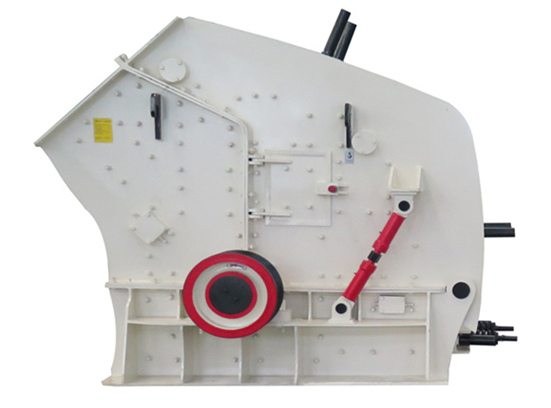
Cone Crushers.
Unlike jaw crushers, cone crushers are efficient in secondary or tertiary crushing. The machine works with the aid of an oscillating shaft, forming a crashing cavity located between the mantle and bowl liner. Gears facilitate the movement of the shaft resulting in continuous compression, thus crushing the objects. The crusher’s working mechanism is adjustable, depending on the level of grinding you want to achieve. First is modifying the main shaft by lifting or lowering it. The second principle is changing the vertical positioning of the concave through rotating the bowl against the threads.
Impact Crushers.
An impact crusher is versatile, thus useful in any level of crushing. It comes in two designs, horizontal shaft impact crusher, and vertical shaft impact crushers. The employed policy for both models is similar, but their features bring out the primary differences. Vertical shaft impact crushers are more efficient in the last stages to achieve a certain cubic level of the end product. Horizontal shaft impact crushers are reliable in primary to tertiary stages. It works with an intensive impact, which originates from the movement of the bars positioned at the rotor. Learn more: https://aimix.my/impact-crusher/
Gyratory Crushers.
Gyratory crushers work using an oscillating shaft to reduce the materials into the right sizes. It has a crushing cavity located between a fixed element on the outer part and an internal movable object. The crushing process’s effect is safe, thus eliminating any risk of wear and tear to the liners. Additionally, the device has a hydraulic system for making necessary adjustments to increase its efficiency. This way, you can crush the materials to different sizes and still get exceptional results.
As seen above, the different types of crushers work to deliver end products through unique procedures. Understanding your needs in-depth will help to select an efficient model.